03/09/2016
- Garand Short Fork Follower Rod
- M1 Garand Short Fork Follower Rod For Sale
- Short Fork Follower Rod
- M1 Garand Short Fork Follower Rod
- Winchester Short Fork Follower Rod For Sale
- Garand Short Fork Follower Rod
Early type milled follower rod with short fork and special machining that accepts the compensating spring. The example above is numbered C-46014 but the majority are un-numbered and also desirable.
- Short Pinion Type 1 Lockbar Rear sight (most rare rear sight as the Type 1 lockbar was only used for a few months) Short Fork Follower Rod Arched Lower Band with solid pin Rare early EMcF stock Grooved rear handguard clip Gas cylinder with front sight seal intact.
- Outpost Armory specializes in the sale of the highest quality M1 Garand rifles, parts and accessories. All parts are original, Winchester, Springfield, HRA, or IHC.
WANTED TO BUY PARTS!!
Our company is constantly looking for additional and new inventory. We still have the “Fastest Check in the East” for your quality original U.S.G.I. M1 Garand, M14, and M1 Carbine parts. Ship your parts (with packing list and contact info) to our retail store for our offer in the form of our business check mailed the same day we receive your parts. We hold your parts intact until your acceptance.
We boast over a 99% satisfied customer record for over the last 30+ Years
****************************************************************************************
WANTED!!!!!!!!!! Parts, bayonets, accessories, catalogs, brochures, old stock certificates, documents, manuals, or any other items produced by or related to the Johnson Automatics Co. Cranston R.I.
****************************************************************************************
Model Shop and specific obsolete Gas Trap early M1 parts.
Yes, we are currently looking for these hard to find elusive parts for our clients. We are authorized to pay top dollar to obtain these items. We are especially in need of any Model Shop bolt, welded seam operating rod, or early gas system components. Model shop bolts are devoid of markings and have a sideways figure 8 shaped ejector hole as viewed from the face. Gas systems are the screw on type. We will pay a large reward for their capture or will pay a handsome finders fee for information leading to our purchasing of these items. We have posted pictures of some of these components below to aid in your identification of these parts.
Above: Left. Early Straight Eared front sight used on gas trap rifles. Notice the ears that straddle the front sight blade are straight. Later on in production the ears were “flared” so riflemen would not mistake one of the straight ears for the front sight blade. The straight eared versions can be numbered B 8882 as pictured above, or B 8882-0. The flared ear version is also numbered with the same drawing number or can be found un-marked. Notice the grooves machined into the sight.
Above: Right. Early numbered B-8876-4 gas cylinder plug. These can also be un-numbered. Several versions exist both with the large hole at the bottom or solid (later production).
Above. Early front handguard ferrule with the lip. These were used on early production M1 rifles that used the early gas system. Notice how a cone shaped appendage protrudes from the face of the ferrule.
Above. Early type milled follower rod with short fork and special machining that accepts the compensating spring. The example above is numbered C-46014 but the majority are un-numbered and also desirable.
Above. Early “Welded Seam” Operating rod. These can be also found without D 28296 number on handle. Notice that the assembly is one piece construction and the handle is not welded to the tube as in later production operating rods.
All Model Shop and Early Part photos above courtesy and copyright Robert Seijas Collection.
We are also interested in other gas trap parts including but not limited to:
Keystone shaped operating rod spring (square wire), compensating spring (square wire), any screw on “gas trap” gas system, early rear sight components, and SA/SPG marked wood or large hole over small hole butt-trap configuration. Any questions??? Just call 631 205 1299 or email Michael@m1garand.com and ask for Michael.
********************************************************************************
Section 5
Paragraphs 19-23
BARREL AND RECEIVER GROUP
19. Disassembly
a. GENERAL. Remove and disassemble barrel and receiver groups (fig. 24) and (fig. 25).
b. REMOVING BARREL FROM RECEIVER (fig. 26). The barrel should be removed from the receiver only when rebarreling is necessary and then only by fifth echelon organizations. To remove, pass the barrel into fixture, muzzle end first, until rib on barrel stops against shoulder in fixture. Position wrench on receiver as near to the barrel as possible and unscrew the receiver (counterclockwise) from the barrel.
Note. Never place the wrench on the rear of receiver, as this will cause distortion.
Garand Short Fork Follower Rod
c. FOLLOWER AND SLIDE ASSEMBLY. Disassemble follower and follower slide (fig. 24) only when repair or replacement of parts is necessary. If necessary to disassemble, insert the blade of a screw driver under front end of slide (fig. 27), pry upward and forward, unlocking slide from follower.
d. GAS CYLINDER GROUP.
(1) Front sight screw. Loosen the front sight screw (fig. 25) before attempting to remove the gas cylinders which have been modified, that is, those having a cut extending from the front sight base dovetail downward to the lower splines. Unless the front sight screw is loosened, damage may result to the barrel and gas cylinder. The front sight screw may be so tight that binding action of the gas cylinder on the barrel will make it difficult to remove the gas cylinder by lightly tapping on the bayonet lug (as described in FM 23-5).
(2) Front sight screw seal. To remove the front sight screw seal (fig. 25), file off its exposed surface, and with a 3/16-inch hexagonal socket head set screw wrench, back out the screw. Replace and tighten the screw.
Note. The seal is no longer required and is not to be replaced after it has once been removed.
(3) Gas cylinder lock. Gas cylinder locks which are extremely tight fitting may be removed by the use of gas cylinder lock assembling wrench. Fit wrench over contour of gas cylinder lock and unscrew (counterclockwise). (See fig. 28.)
e. REMOVING AND INSTALLING EXTRACTOR WITHOUT REMOVING BOLT FROM RIFLE. (fig. 29). To remove or install the extractor without removing the bolt from the rifle proceed as follows, using bolt, wire brush, and screw driver combination tool:
(1) Retract the bolt and insert the wire brush into the chamber of the barrel until the shoulder of the tool bears against the breech end of the barrel.
(2) Allow the bolt to close slowly, turning the tool so that the lug is under the extractor.
(3) Force the operating rod forward, holding the bolt against the tool, and turn the combination tool counterclockwise so that the lug pushes the extractor out of its seat and out of engagement with the ejector.
(4) Retract the bolt slowly, thus allowing removal of the extractor spring plunger assembly and cartridge ejector assembly. The firing pin can then be withdrawn from its well.
(5) To install, place ejector and ejector spring, extractor and extractor spring in the bolt. With the brush of the combination tool in the chamber, line up the notches of the firing pin and ejector and force the operating rod forward, compressing ejector spring. While holding spring compressed, press extractor into position.
20. Inspection
a. GENERAL. Inspect all parts for damage, wear, burrs, rust, foreign matter in recesses, deformation, and for function and free action with mating parts. Important points to be inspected are shown in figures 30 and 31. Test all springs for set, minimum free length, and fracture.
b. FOLLOWER ROD. Inspect follower rod (fig. 31) for a pinched or worn fork and for loose rivets. The follower rod should have a long fork; therefore, replace all rods having short forks. (See fig. 32) This is necessary to prevent the rod from disengaging when grenades are being launched. Dispose of the old type (short fork) follower rod in accordance with existing regulations for unserviceable equipment.
M1 Garand Short Fork Follower Rod For Sale
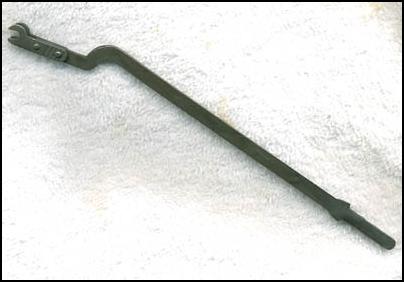
c. OPERATING ROD SPRING (fig. 24). Inspect the operating rod spring for free length and load in the following manner, using operating rod spring gage:
(1) Testing free length. Insert the operating rod spring in tube of gage and raise rod until bottom of stop collar is flush with top surface of gage. (See fig. 33) Note position of operating rod spring in regard to top face of tube. If spring does not protrude beyond top face of tube, the maximum free length of 20 1/4 inches is satisfactory and the spring is serviceable in regard to free length. With the spring still in the tube, allow the rod to return to its original position and test for load.
(2) Testing load. Insert the stem of the 5-pound weight in tube of gage and allow its weight to compress the spring. It should compress between 16 3/4 and 17 3/4 inches which is indicated by the first 1-inch relief notch cut in the stem of the weight. Note position of this notch in regard to top face of tube. If top face of tube falls within the limits of the relief notch (fig. 34), the load at 5 pounds is acceptable. Next position the 11-pound weight on top of the 5-pound weight and allow their combined weight to compress the spring. It should compress between 11 3/4 and 12 3/4 inches which is indicated by the second 1-inch long relief notch cut in the stem of the 5-pound weight. Note position of this notch in regard to top face of tube. If top face of tube falls within the limits of the notch (fig. 34) the load at 16 pounds in acceptable.
d. OPERATING ROD (fig. 30). Inspect for binding between the barrel and receiver group and the operating rod by installing the rod and bolt in the rifle. As the rifle is tipped up and down, the rod and bolt should be moved from closed to open position and back by their own weight. If there is binding, inspect the tube for dents and the handle for deformation, which will cause binding of the under side of the lug on the cut in the receiver. Inspect the piston for scoring and the accumulation of excessive carbon. Inspect the diameter of the piston using no-go piston gage. (See fig. 35) All no-go piston diameter gages, initially produced are being withdrawn from service for reworking since the dimension of these gages has proven unsatisfactory. Pending the correction of these gages, the piston diameter will be measured with a micrometer and pistons which measure 0.525 inches or more should be considered unserviceable. If the piston diameter is below the minimum specified by the serviceability chart (fig. 23), the operating rod assembly should be disposed of as unserviceable and uneconomically reparable, since an undersized gas piston tends to reduce the power available to operate the weapon.
e. FOLLOWER AND FOLLOWER SLIDE (fig. 30). Inspect slides on follower for correct angle. An angle of approximately 92° ± 0° 20 minutes must be maintained. (See fig. 36.)
f. REAR SIGHT PINION - EARLY MANUFACTURE. Inspect the pinions visually. Pinions having cracks caused by staking will not be removed from service (fig. 37), provided they do not interfere with functioning.
g. GAS CYLINDER GROUP (fig. 38). Check the inside diameter of gas cylinder with gas cylinder gage. When the threads are cut in the gas cylinder the metal tends to flow and the inside diameter of the threaded section is reduced; therefore, this section must be slightly reamed to allow the gage to be inserted. Use the reamer on one end of the gage to perform this operation. Only the wire edge on top of the threads is removed. Remove all chips after reaming; any chips remaining will cause galling between the gas cylinder and the gas cylinder lock screw, due to the nature of stainless steel. Insert the gage after reaming and if the cylinder is serviceable the index surface of the gage should be level with, or protrude above, the end of the gas cylinder. (See fig. 39).
Caution: No force must be applied to a gage when a cylinder is being checked. If the gage is forced in the cylinder and rotated it will act as a reamer and will render the gas cylinder unserviceable.
Insert a small rod in the screw driver end of the gas cylinder lock screw and raise the valve from its seat. Inspect for burrs and foreign matter. This is an important check as gas allowed to escape through the valve will dissipate the force necessary to drive the operating rod to the rear, thus causing a short recoil malfunction. Inspect function of valve spring to see that it closes the valve tightly in its seat. Replace all gas cylinder lock screws which have burrs on the valve face or seat, or where the spring tension is insufficient to seat the valve tightly. All gas cylinder lock screws of early manufacture should be replaced by gas cylinder lock screw with valve assembly.

h. BOLT ASSEMBLY (fig. 40).
(1) Bolt. Test the bolt while it is free for freedom and smoothness of movement and for locking.
(2) Firing pin. Check protrusion of firing pin beyond the face of the bolt using firing pin protrusion gage. (See fig. 41) In fired position, the nose of the pin should protrude from 0.044 inch minimum to 0.059 inch maximum. Remove all full round firing pins and discard in accordance with existing regulations.
(3) Extractor. Test the extractor for grip on the cartridge base, and the extractor spring for tension.
i. BARREL. Inspect the barrel as outlined in Section II
j. TELESCOPE MOUNT AND BRACKET (U.S. Rifle, Cal. .30, M1C (Sniper's) ONLY). (fig. 42 and fig. 43). Inspect telescope mount bracket for retention on receiver and for burrs on male dovetail slides. Inspect slide for function in telescope mount bracket and locking action of slide clamp with locking screws. Check supports for looseness in slide. Inspect screws and screw holes for worn or stripped threads and all recesses for foreign matter.
k. TELESCOPE MOUNT AND BASE (U.S. Rifle, Cal. .30, M1D (Sniper's) ONLY). (fig. 44). Inspect base for looseness on barrel, and for burrs. Inspect dowel pin for burrs, wear, and for looseness in base. Inspect knob for looseness on screw and for worn knurling. Inspect function of plunger and spring with knob. Check bracket and hinge for clamping action with telescope. Inspect all screws and screw holes for stripped or worn threads.
21. Maintenance and Repair, Third and Fourth Echelons.
a. CORRECTING ANGLE OF FOLLOWER. If angle on follower is not within the required limits (fig. 36), bend slides to correct angle by lightly tapping with a brass hammer.
b. OPERATING ROD.
(1) The operating rod tube (fig. 24) is slightly offset to provide clearance at the enlarged portion of the barrel. This offset is not be changed. When the operating rod is assembled to the rifle by the manufacturer, the operating rod is fitted to its respective rifle by bending.
Note. This is an operation requiring considerable training and is not practiced by field organizations. For this reason operating rods should not be exchanged among rifles if it can be avoided.
(2) Remove all rust and accumulated carbon from the tube with a fine abrasive or rifle bore cleaner.
Caution: Exercise extreme care to prevent rounding the edges or reducing the diameter of the piston. Do not use emery or other abrasives on this component because no shine or polish is necessary on the piston.
c. GAS CYLINDER.
(1) To remove accumulated deposits of carbon from the gas cylinder, remove the lock screw and remove the carbon with the screw driver blade of the combination tool or a similar instrument. The gas cylinder lock may be removed and the screw reinserted in the gas cylinder and threaded in far enough to break loose the carbon. Exercise care not to cross the threads. The gas cylinder port can be cleaned with a straight punch or the drift on the combination tool. The inside of the gas cylinder is to be thoroughly wiped clean and oiled. A few drops of oil placed between the rear gas cylinder lug and the operating rod, with the muzzle tipped down, will be sufficient. Hand operate the rod through a few cycles to distribute the oil properly. Remove any rust on the outside of the cylinder, using rifle bore cleaner or fine abrasive. Remove rust on the barrel at this point in a similar manner.
(2) If the bayonet lug is worn to a loose fit with the ways in the bayonet, the lug may be peened lightly to provide a better fit. Rest the lug on a solid surface when peening.
d. GAS CYLINDER LOCK.
(1) Excessive thickness. Difficulty may be experienced in fitting the bayonet to the rifle due to excessive thickness or lack of concentricity of the gas cylinder lock. (See fig. 38) This is rectified by grinding or filing the portion of the gas cylinder lock that fits inside the bayonet guard.
(2) Installation. Position the cylinder on the barrel. (See fig. 38.) Screw gas cylinder lock down as far as possible by hand. Do not force. Unscrew the lock until the screw hole in the lock lines up with the threaded hole in the gas cylinder, permitting assembly of the gas cylinder lock screw. In some cases, the lock will have to be unscrewed almost a full turn. Turn screw in several threads with fingers only. Push the gas cylinder lightly toward the muzzle until it rests against the lock and tighten screw.
e. REAR SIGHT ASSEMBLY.
(1) General. The rear sight assembly of present manufacture (fig. 46) offers no unusual maintenance problems, but differs from sights of early manufacture (fig. 45) in that the elevating pinion and windage knob have been replaced by assemblies. The elevating knob assembly replaces the elevating pinion, elevating knob, and elevating screw. This assembly cannot be disassembled and no attempt is to be made to disassemble it. If refinishing is required, it is to be refinished as a unit. The windage knob assembly will be handled in the same manner. This assembly replaces the windage knob, the rear sight nut, rear sight nut lock, and rear sight nut lock spring. The new assembly is designed to overcome the requirements for loosening and retightening the rear sight nut between sight settings. In the case of this sight, the pinion is not to be staked after assembly.
(2) Staking rear sight pinion - early manufacture. When assembly and final adjustments of the rear sight of early manufacture are completed, lightly stake the rear sight pinion as shown in figure 47, to prevent the nut from becoming lost in service. An automatic punch, if available, can be used to better advantage than rear sight pinion punch when performing this operation.
Note. Place a lead bar or piece of hard wood under the elevating knob before staking so as not to damage rear sight assembly.
f. BARREL.
(1) Rust on barrel. Remove rust from the side of the barrel by rubbing with a cloth and wiping with preservative lubricating oil (special). If this is not sufficient, use crocus cloth lightly, taking care not to produce a shiny surface. Make certain that there is no rust or foreign matter in the gas port and where the gas cylinder contacts barrel. The outside diameter of the barrel at bearing for gas cylinders must not be reduced, since any leakage of gas between the barrel and gas cylinder greatly reduces the power available to operate the weapon and, therefore, promotes short recoil stoppages. Check diameter after cleaning with barrel diameter at gas port gage. (See fig. 48)
(2) Carbon in gas port. The gas port in the rifle barrels is not to be enlarged. It is permissible to remove carbon, corrosion, or fouling, which may have accumulated, by passing a 0.0805-inch drill through the port.
Note. It is not to be drilled larger than 0.0805 inch.
If the port is increased in diameter to make one rifle function, and the gas cylinder is replaced at a later date by a cylinder manufactured to the extremes of drawing tolerance, which tends to increase the power of the rifle, a malfunction may occur. The bolt speed will increase, increasing the force with which the bolt strikes the rear of the receiver. The bolt then bounces off the receiver with such speed that the ammunition may not have time to reach the feeding position, and a feed stoppage occurs. Occasionally the added velocity of the bolt is sufficient to break the receiver, which would be a definite hazard to the firer.
g. TELESCOPE MOUNT AND BRACKET (U.S. Rifle, Cal. .30, M1C (Sniper's) ONLY). A fine-grained, three-cornered sharpening stone or fine, three-cornered file may be used to remove burrs from the male and female dovetail slides. Replace screws which are stripped or worn to a loose fit.
22. Maintenance and Repair, Fifth Echelon.
Short Fork Follower Rod
a. OPERATING ROD MODIFICATION.
(1) The operating rod modification provides a radius at the corner in the operating rod near the operating rod catch notches (fig. 49) to prevent the development of a crack in this section.
(2) Use a 3/16-inch end mill of conventional design in performing this modification.
(3) Mount the operating rod on the table of the milling machine with the flat section, on which the drawing number is stamped, perpendicular to the axis of the cutter. Ascertain starting point of cut with scribe line on improvised depth gage. (See fig. 20) Start the cut at the rear end and travel forward on rod until the specified radius is produced.
Note. It is essential that the marks of the cutter be lengthwise with the rod rather than perpendicular to it, as any mark running perpendicular will localize stress and form a starting point for fatigue cracks.
Do not use any method of machining that will make scratches or machining marks perpendicular to the rod. Be careful not to remove more material than that specified in drawing. (See fig. 49)
(4) Use the improvised height and depth gages (fig. 19 and 20) to check cut. The gage shown in figure 50 is a maximum-minimum gage to check depth of cut in the handle section of the operating rod. The gage shown in figure 51 is a maximum-minimum gage to check forward travel of the cutter, starting point of cut. With the gage in position on the rod, origin of cut should fall within width of solid line scribed on gage.
b. REFINISHING SHINY GAS CYLINDER.
Rifles with shiny gas cylinders must not accompany troops to oversea bases. The gas cylinders, gas cylinder locks, and gas cylinder lock screws of these weapons are machined from stainless steel. Normal methods of blackening these components, such as penetrating (application of black finishing oxidizing material) or parkerizing, are ineffective; therefore, if no special processes are available (see TM 9-1861), refinishing of the gas cylinders must be performed by painting, using the following procedures:
(1) Remove all old paint, and make certain the surfaces of the parts to be painted are free from grease or other foreign matter.
(2) Assemble the gas cylinder lock to the gas cylinder, securing it with the gas cylinder screw.
(3) Paint the shiny parts with a mixture of flat black paint thinned with synthetic enamel thinner in the ratio of 2 ounces of thinner to 1 quart of paint. Both are listed in ORD 3 SNL K-1 and may be requisitioned from Raritan and Benicia Arsenals. The paint may be obtained in quart cans; 1 quart will paint approximately 250 gas cylinders. The thinner may be obtained in 1/2-pint cans; 1/2 pint is enough for approximately 1 gallon of paint. Have some additional thinner on hand to clean the paint brushes or spray guns, and for thinning old paint. Be certain that the paint and thinner are mixed thoroughly, then apply with a spray gun or a small, flat paint brush. Take care to prevent paint from running into the gore of the gas cylinder.
(4) Place the painted assembly in an oven (fig. 52) and bake for 1 1/2 hours at a temperature of 300 degrees F. To prevent drying or charring of soft materials, the heat is not to be greater than the maximum temperature prescribed. The baking may be accomplished in any type of improvised oven and in conjunction with any available source of heat capable of producing a relatively low temperature of 300 degrees. An oven for baking purposes can be improvised from sheet iron; or, if this is impossible, an ordinary domestic-type, kerosene stove oven may be used. The oven may be heated electrically, by gasoline, or by oil, and may be used in conjunction with a field range or portable stove.
Caution: Care must be used to prevent the parts from being subjected to direct or open flame.
(5) When properly applied, the resultant dead-black finish which does not reflect light will be hard, durable, unaffected by the normal heat of the weapon, and highly resistant to abrasion. This method may also be used to blacken other nonfunctioning exterior surfaces, such as folding metallic stocks, butt plates, front sights, sling swivels, and other small parts.
c. BARRELL REPLACEMENT.
(1) Disassembling. Separate the unserviceable barrel from the receiver, as described in paragraph 19b
(2) Assembling. Without using undue force, screw barrel on receiver by hand until it fits tightly. The receiver should be approximately 15 degrees out of its correct position on barrel to insure a tight fit when final draw is made in the carrel and receiver assembly fixture. Clamp the group in the barrel and receiver assembly with three clamps, tightening the lower clamp first to level receiver. (See fig. 53.) Slide key, located on the indicating arm of the fixture, into the upper gas cylinder spline cut as far as it will go. Pull on the lever, thereby turning the barrel the required distance to bring the indicator to agreement with the qualifying line on the fixture.
Note. Pointer must travel the distance from within lower space cut to qualifying line cut (Fig. 53) to insure a tight fit,
Then loosen the locking clamps and remove the assembly from the fixture, using a bar placed through the trigger housing opening in the receiver to start the assembly from the fixture.
(3) Checking barrel and receiver assembly fixture. Check the barrel and receiver assembly fixture (fig. 13) monthly or oftener if necessary to see that barrels are being alined properly. To make a check, use a barrel and receiver that has been assembled in the fixture and slip the barrel alining gage with pin (fig. 9) over the splined portion of the barrel. (See fig. 54) For this test select a barrel which allows no side-ways play of the gage in the spline cut. Insert a 3/8-inch rod through the rear sight pinion holes and suspend the receiver on a pair of parallels or V-blocks just high enough to clear surface of plate, Elevate the muzzle to a level position and block up. Levelness can be found by using the dial indicator on top surface of the gage in the direction of the center line of the barrel. Now using the dial indicator, gage the top surface of the barrel alining gage on the end of the muzzle. If the top surface of the barrel alining gage is parallel to the surface place, the alinement of the barrel and receiver is correct.
Note. A properly alined barrel should be ± 0 degrees 20 minutes (± .0058 per inch on top surface of barrel alining gage) to the horizontal plane of the receiver. (See fig. 55.)
(4) Looseness of barrel in receiver. If the barrel screws into receiver by hand within 7 degrees of its assembled position, it is considered to have 'light draw'. This may be corrected by placing barrel and receiver in assembling fixture and assembling properly. Remove it from the fixture and chuck barrel in a lathe, with the receiver being as close to the chuck as possible. Allow room for the swaging roll. (See fig. 18.) With the roller in tool post, roll the barrel. (See fig. 56.) The edge of the roller should be 1/4-inch away from the receiver. Do not loosen the barrel after rolling, as rerolling will be necessary.
d. HEADSPACE REAMING.
(1) Wipe the chamber thoroughly with a cotton flannel patch before and after each reaming, and prior to each headspace check during reaming. Screw the short adapter (fig. 11) deeply into the reamer and tighten lock nut. Dip the reamer in lard oil and insert it into the reamer guide. Make certain bolt lug recesses in receiver and bolt lugs on reamer guide are free from dirt and foreign matter. Place the guide and reamer in the receiver (fig. 57) and tighten thumb screw to hold guide in position.
(2) Attach the universal-jointed extension to the reamer and rotate it with a chuck.
Note. If the reamer has been correctly assembled to the adapter it will not cut, but will be held away from the chamber by interference between a should in the guide and the adapter.
Unscrew the adapter from the reamer a little at a time until the reamer begins to cut. Adjusting the headspace reamer is accomplished by loosening the locking nuts, and backing off or advancing the adjusting screw a little at a time, using the field test bolt (fig. 7) and headspace gage name in the serviceability chart (fig. 23) to check for proper adjustment.
When the adapter is correctly adjusted in the reamer, check the tightness of the locking nut. The reamer, once it is adjusted, and if carefully used, will continue to ream to the same dimension until the reamer becomes dull and must be replaced or sharpened.
M1 Garand Short Fork Follower Rod
Note. Any reaming beyond the minimum limit of 1.940 inches reams away a part of the headspace life of the assembly; therefore, make certain all reaming is held to as near the minimum as possible.
Never turn the reamer backward, as such action will chip the lands. Use liberal quantities of lard oil when reaming and wash all chips from the reamer with lard oil each time it is removed from the work. Sharpening stones are furnished for the purpose of keeping the reamers honed properly. Proof fire every rebarreled rifle.
Winchester Short Fork Follower Rod For Sale
23. Assembly
a. GENERAL.
(1) Assemble in accordance with instructions contained in FM 23-5.
(2) Assembly of parts covered in the following paragraphs is performed only by ordnance personnel and therefore not covered in FM 23-5.
(3) Methods used by fifth echelon organizations for assembling parts in mass rebuild are also covered in the following paragraphs.
b. FOLLOWER AND SLIDE ASSEMBLY. To assemble, hook the slide in place in the small end of the follower. Stand the two pieces on end (fig. 58) or mount them at an angle in a vise. With a soft hammer deliver a sharp blow on the reamer end of the slide. It will then snap back into position on the follower.
c. ASSEMBLING BARREL TO RECEIVER. Refer to paragraph 22c for assembly of barrel to receiver.
d. BOLT ASSEMBLY. The use of the bolt assembling fixture (fig. 13) is the easiest method of installing the extractor (fig 59) when a large number of bolts are being repaired. Install the firing pin, extractor spring, and extractor plunger, also ejector spring and ejector in bolt and clamp bolt in extractor assembling fixture. Start extractor in bolt and tap in place with a soft hammer.
Note. This fixture can also be used to remove the extractor.
e. ASSEMBLING EJECTOR, EXTRACTOR, AND REAR SIGHT SPRINGS. When rebuilding large quantities of rifles, fifth echelon organizations will find the ejector assembling fixture (fig. 13) a useful tool for assembling the ejector, extractor, and rear sight springs to their respective components. To use, select the proper spindle and bushing corresponding to the components being assembled. Place the spring in the aperture in the spindle and its related component in the bushing. (See fig. 60) Press forward on knob until component is inserted in spring.
f. ASSEMBLING REAR SIGHT. When assembling or disassembling large quantities of rear sights, use the windage screw knob wrench. (See fig. 12) Fit the adjustable split socket over the windage or elevating knob and tighten thumb screw. Use crank to facilitate rotating of the rear sight knobs.
[Back to TM 9-1275 'INDEX']
Section
- INTRODUCTION
-INSPECTION PRIOR TO DISASSEMBLY
-TOOLS, GAGES, AND FIXTURES
-GENERAL MAINTENANCE
-BARREL AND RECEIVER GROUP
-TRIGGER HOUSING GROUP
-STOCK AND HAND GUARDS
-EQUIPMENT
Garand Short Fork Follower Rod
-FUNCTION FIRING AND FINAL INSPECTION
-MALFUNCTIONS AND CORRECTIONS